Livscyklusanalyse af metalslagge
Gennem livscycklusanalyse giver projektet data om state of the art genvinding af metaller i dansk slagge, potentialet for yderligere genvinding samt de miljømæssige fordele og ulemper.
Metal recovery from Municipal Solid Waste Incineration Bottom Ash (MSWIBA): state of the art, potential and environmental benefits
Elisa ALLEGRINI1, Maria S. Holtze2, Thomas F. ASTRUP1
1Department of Environmental Engineering, Technical University of Denmark, Building 113, DK-2800 Lyngby, Denmark. 2AFATEK Research Centre, Selinevej 16, DK-2300 København, Denmark
Abstract
Incineration has a central role in the waste management system in Denmark (e.g. 52% of the household waste) resulting in approximately 726000t of solid residues each year. However, the targets imposed by the Danish Waste Strategy and the increasing discussions about resource in waste raise an issue on resource losses through waste incineration. In this framework, this study provides actual data on the state of the art of the recovery of resource in MSWIBA in Denmark (i.e. metals), on the potential for further recovery and on the environmental benefits or burdens assessed through the Life Cycle Assessment (LCA) methodology.
Introduction
The Danish Environmental Protection Agency reported that in 2009 24% of the total waste generated in Denmark was incinerated (1). This resulted in the production of approximately 726000t of solid residues.
Bottom Ash (BA) accounts for approximately 90% of the total solid residue (2). The rest includes boiler ash, fly ash and air-pollution-control residues, and it is classified as hazardous waste, thus disposed after stabilization pre-treatments. BA is not hazardous waste and, after pre-treatment (i.e. metal recovery and ageing), is recycled as aggregate surrogate in construction works (3).
The increased attention towards the loss of resource in waste streams as well as economic factors (e.g. metals prices) drove environmental stakeholder towards an optimization of the recovery of resources in waste. In countries where incineration represents a relevant treatment option there is an increasing interest in trying to recover as many valuable resource from the resulting solid residues. Up to date, the main focus has been given to the metals scraps in the BA, mainly ferrous (Fe) and non-ferrous (NFe) metals, recoverable through mechanical processes and then directly recyclable in the metallurgical sector (e.g. 4, 5, 6). However, many studies also focus on the recovery of metals (e.g. Cu) through methods other than mechanical (e.g. 7). Attention is recently also being given to minor fractions of the NFe metals such as the precious metals (e.g. 8) but also to other metals such as the rare earth metals defined critical because of their important role in the information and green technologies and for their short term supply risk due to geopolitical factors (e.g. 9, 10).
The goal of this poster is to present the current state of the art of NFe metals recovery from BA in Denmark, to assess the potential for further recovery, and to introduce the future works about implementing metal recovery systems of increasing complexity in a life cycle assessment (LCA) perspective.
Material and Methods
The study was based on the metal recovery system developed by AFATEK and treating BA produced at six municipal solid waste incinerators in Denmark. The system consists of: Fe metals recovery section, where the BA is sieved at 50mm and the two resulting streams undergo magnetic separation; NFe metals recovery section, where the BA below 50mm is sieved in the fractions 50-16mm, 16-8mm, 8-2mm and <2mm and, all the fractions above the 2mm are treated by means of Eddy Current Separators (ECS) and, the fraction 50-16mm is further treated in an Inductive Sorting System (ISS) to recover stainless steel (SS); upgrading systems for the recovered Fe and NFe fractions. The two upgrading systems rely only on mechanical treatments based on sieves, magnets, ECS, ISS and density separators.
Data on the content of metals scraps were based on laboratory tests carried out on 21 samples of BA collected before the NFe metal recovery system and on two samples collected after the same system. The laboratory procedure used was based on the procedure developed at the Swiss Institute for Environmental and Process Engineering (UMTEC) based on a series of crushing and sieving operations, aimed at liberate and then separate the metals from the slag. The metals collected are then separated into Fe and NFe using a magnet. The samples were also analyzed for moisture content and grain size distribution by the use of standardized stainless steel sieves. Additional data on the operational conditions of the system and on the yield of metals after the upgrading processes were provided by AFATEK.
The data were used as input to the software STAN, developed at the University of Technology of Vienna, in order to carry out a mass flow analysis (MFA) and substance flow analysis (SFA) of the BA management system.
Results and Discussion
Figure 1 reports the results of the MFA and SFA analysis. It is seen that the NFe scraps in the raw BA accounted for approximately 2.2%ww, which is similar to values reported in literature (e.g. 4, 11, 12). Concerning the total efficiency of the system, approximately 62%ww of the total NFe in the raw BA is actually recovered; this is in agreement with current recovery efficiencies achieved in other countries (e.g. 13). In the fraction treated at the NFe recovery system (“residue 2-50mm” in Figure1) the losses of NFe were ranging between 1 and 13%ww. As shown in Figure 1, the resulting flow of NFe metals for the stream “residues 2-50mm” was characterized by large standard uncertainty. Laboratory data for the mentioned flow were not entered in the model, but they were used for cross-checking and validation of the results. The data used as input were those based on a large number of analysed samples, thus considered to be robust. However, additional data will be collected, thus further MFA and SFA will be performed.
The largest loss was found to be in the not-treated fine fraction (<2mm) representing approximately the 32%ww of the total raw BA and presenting a content of NFe metals of 2.4%ww. New developments of the systems will address the recovery of NFe in this fraction that is particularly critical in BA undergoing wet quenching at the incinerator (14): the high moisture content makes the segregation of different grain size fractions and the recovery of metals from there difficult.
Moreover, other issues have to be taken into account besides those strictly related to the recovery technology. What is the quality of the recovered metals in the fine fraction? Is the oxidation level of the fine fraction too high to make the recovery worthy? How much energy and resource need to be invested to recover more metals? In the current system the only input in terms of energy and resource is electricity and diesel, and calculating the carbon footprint of the system considering only the reprocessing of the recovered Al and the subsequent avoided primary production, the net saving results of 305tCO2-eq/5000tBA. The environmental convenience of the current system is undeniable also because it is based on simple mechanical treatment that does not use chemicals or other resource and does not produce hazardous waste streams.
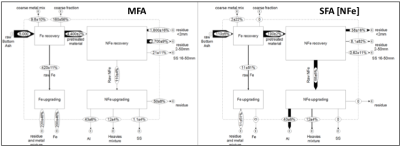
However, to recover increasing amount of metals the complexity of the treatment system will increase as well as the amount of invested resource and energy, and the ratio between the recovered resources and the related investments will exponentially decrease. Thus, it is important to implement the metal recovery from BA in a LCA perspective including systems of increasing complexity to identify the optimum point between the benefits from metal recovery and the burdens to the environment. An LCA contest allows including all the aspects of the treatment system, including the utilization or the disposal of the resulting slag (taking into account the leaching aspects) or the production and then the handling of possible new waste streams.
References
- Miljøstyrelsen - Affaldsstatistik 2009 og Fremskrivning af affaldsmængder 2011-2050, 2012.
- A.J. Chandler, T.T. Eighmy, J. Hartlen, O. Hjelmar, D.S. Kosson, S. Sawell, H.A. van der Sloot, J. Vehlow, Municipal Solid Waste Incinerator Residues, Elsevier, 1997.
- T. Astrup, “Pretreatment and utilization of waste incineration bottom ashes: Danish experiences”, Waste Management, 27, 1452-1457 (2007).
- L. Muchová, P. Rem, “Metal content and recovery of MSWI bottom ash in Amsterdam” WIT Transactions on Ecology and the Environment, 92, 211-216 (2006).
- S. Heinrichs, B. Wens, A. Feil, T. Pretz, “Recovery of nf-metals from bottom ash’s fine fraction - state-of-the-art in Germany”, in Proceeding of Fourth International Symposium On Energy From Biomass And Waste, 12-15 November, Venice, Italy, 2012.
- M. Grosso, L. Biganzoli, L. Rigamonti, “A quantitative estimate of potential aluminium recovery from incineration bottom ashes”, Resour. Conserv. Recycling, 55, 1178-1184 (2011).
- K.K. Fedje, “Metals in MSWI ash-problems or opportunities?”, in Proceeding of Ash Utilisation 2012: Ash in a Sustainable Society, January 25-27, Stockholm, Sweden, 2012.
- L. Muchova, E. Bakker, P. Rem, “Precious Metals in Municipal Solid Waste Incineration Bottom Ash”, Water Air Soil Pollut, 9, 107-116 (2009).
- L.S. Morf, R. Gloor, O. Haag, M. Haupt, S. Skutan, F.D. Lorenzo, D. Böni, “Precious metals and rare earth elements in municipal solid waste-Sources and fate in a Swiss incineration plant”, Waste Management, in press (2012)
- F. Zhang, S. Yamasaki, K. Kimura, “Rare earth element content in various waste ashes and the potential risk to Japanese soils”, Environ. Int., 27, 393-398 (2001).
- G. Mitterbauer, S. Skutan, H. Rechberger, “Contents and variability of recoverable metals in MSWI bottom ash”, in Proceeding of the 3rd BOKU Waste Conference: Prosperity Waste and Waste Resources, April 15-16, Wien, Austria, 2009.
- J.M. Chimenos, M. Segarra, M.A. Fernández, F. Espiell, “Characterization of the bottom ash in municipal solid waste incinerator”, J. Hazard. Mater., 64, 211-222 (1999).
- W. De Vries, P.C. Rem, M. De Keizer, ”Value creation out of MSWI bottom ash”, in Proceeding of WASCON 2012 – towards effective, durable and sustainable production and use of alternative materials in construction. 8th International conference on sustainable management of waste and recycled materials in construction, 30 May – 1 June, Gothenburg, Sweden, 2012.
- ZAR (stiftung zentrum für nachhaltige abfall- und ressourcennutzung), Technischer Statusbericht Thermo-Recycling, 2011.